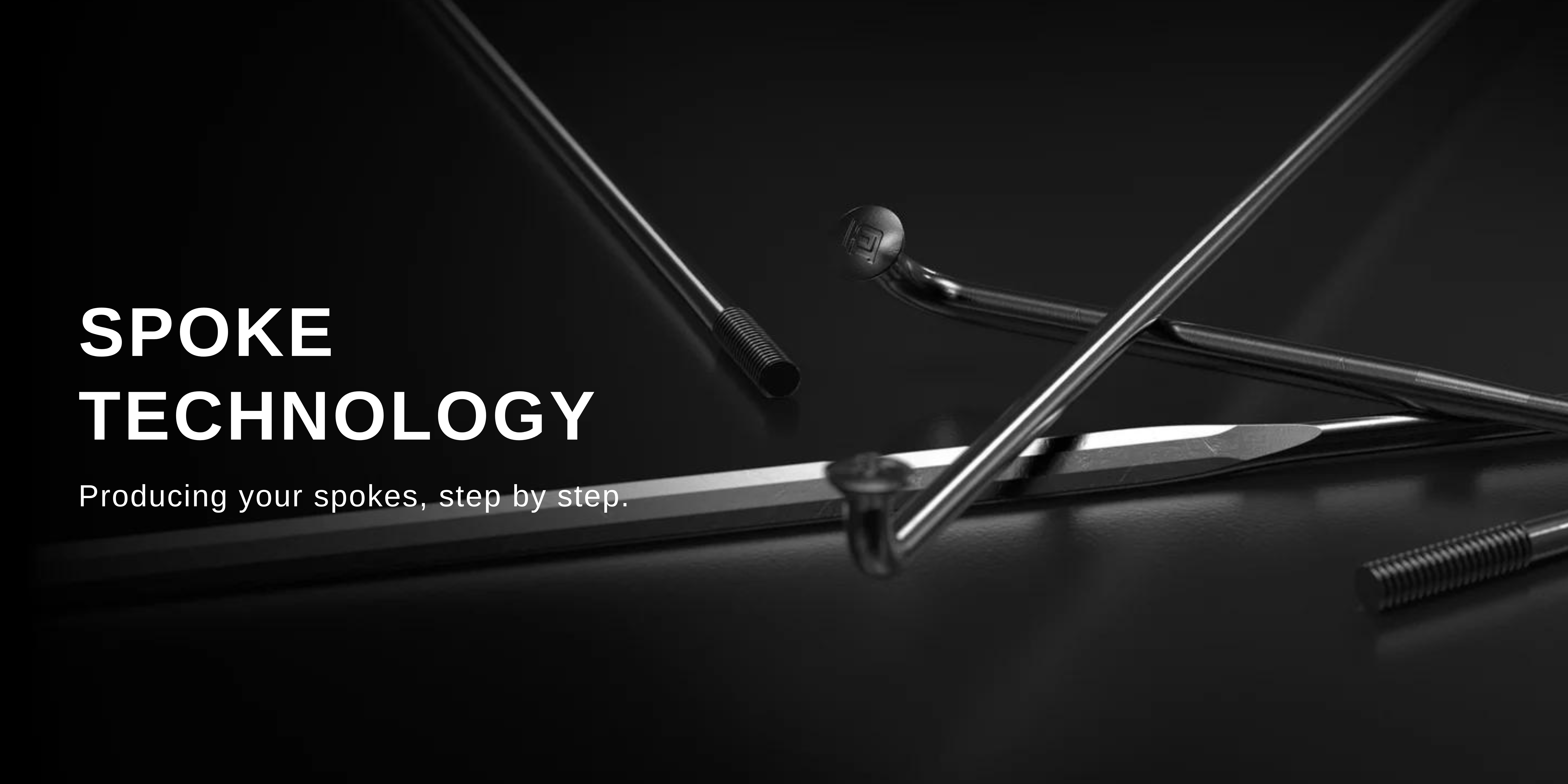
STEEL RAW MATERIAL
Steel alloy specially processed for the manufacture of spokes is drawn from selected wire suppliers. This raw material has to be a consistent high quality which gets controlled consistently.
A spoke will undergo a certain variety of alterations, which is why a specific alloying of the steel allows the wire to be further processed to the required strength and elongation properties of the spoke wire. The quality control is essential from here on, the delivered raw material must be in accordance with the specifications required by DT Swiss with regard to its composition and quality.
RAW MATERIAL WIRE
The delivered 18/10 stainless steel spoke wire has already undergo bending and tensile tests at the outgoing department of the supplier. The spoke wire is wound into spools (coil) of approx. 600-700kg and are delivered in 4 different diameters: 1.8, 2.0, 2.15 and 2.34 mm. The close exchange and coordination of product control between DT Swiss and the wire supplier make sure the tight tolerances of the surface, the diameter and the ovality of the wire are maintained. By complying with the specifications, an efficient and machine-friendly production of the spokes can be guaranteed. The outgoing goods inspection of the supplier is identical with the incoming goods inspection of DT Swiss. In order to ensure a smooth surface, it is with a simple touch of the hand that the tests are conducted , on the surface of the coil. The diameter and the ovality are then controlled with a micrometer.
SPOKE STRAIGHTENING
The wire is unwound directly from the coils and straightened by machine and cut to length to form spoke blanks. This step is performed for all spokes and results in straight spoke blanks precisely cut to length in the hundredths range. Here, the most important control is not only made on the material, but the machine and its wear. Each machine in the production is checked twice a day with different measuring tools featuring tight tolerances in order to ensure a constant quality and finish of the material. This control is very important for the smooth flow of the subsequent processing steps.
COLD FORGING
This process, which was developed and patented by DT Swiss, is used to reduce the desired diameter of the spokes. By rotating oscillating hammers around the wire, the spoke blank is compressed and reduced in diameter. This process results in a spoke that is both light and strong, with a butted elastic part for lightweight and a firmer head and thread for higher loads capacity.
Thanks to the cold forging process, the material is strengthened while retaining its good elongation properties. The transition from a reduced to unreduced diameter of a spoke is extremely harmonious and generates a high-quality appearance . Before the next step, a selection of spokes are hand checked for straightness, diameter and ovality.
FORMING HEAD AND THREAD
As the steps progress, the product gets closer to its known form. The spokes are cut to an exactly calculated and desired dimension. Directly thereafter, the spoke head is embossed together with the unique “DT” symbol. Classic spokes are additionally cranked in a 90-95° angle. At the other end of the spoke blank, the thread is formed in the rolling process. This ensures the correct length, the J-shape for Classic spokes and leads to a material reinforcement on the thread which simplifies the wheel construction and increases the strength.
Several checks are then performed on the spokes. An optical inspection of the spoke head ensures that the logo is visible, and that the material has no defects on its angle. The head diameter, angle length and thread (length and diameter) are measured with a digital caliber. The spoke thread faces a manual function test. The last measurement is a zero point measurement with Trimons Altimeter. This series of tests is performed every 35 minutes on at least one spoke.
FLAT FORGING
The source material is straight gauge or cold-forged spokes, which are bladed during this process with a weight of up to 200 tons. This flat shape of the spoke provides particularly aerodynamic advantages. The forging process densifies the material even more, which in turn achieves a greater strength. An inspection of each spoke is made to ensure the correct length and its flat part, this quality control is performed every 15 minutes.
SPOKE BLACKENING
For aesthetic reasons, the spokes can also be blackened. Although it may seem simple, this blackening process is quite specific to ensure that coloring of the spokes does not add extra weight or performance penalties. For each order, a selection of spokes is tested on the quality of blackening to ensure optimal resistance even after several years. About 85 % of the spokes that leave the factory are black.
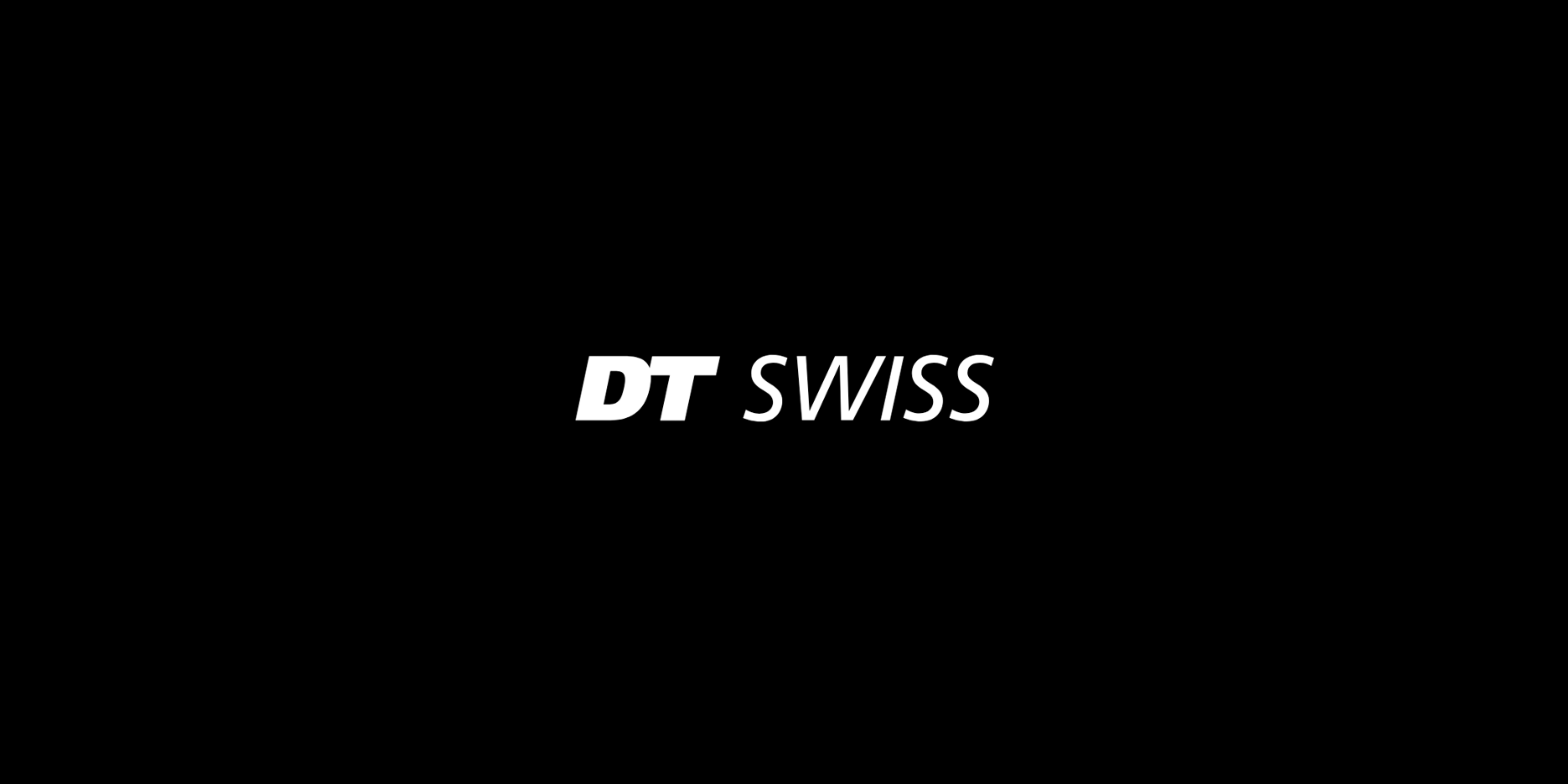